The Crucial Role of Post-Processing
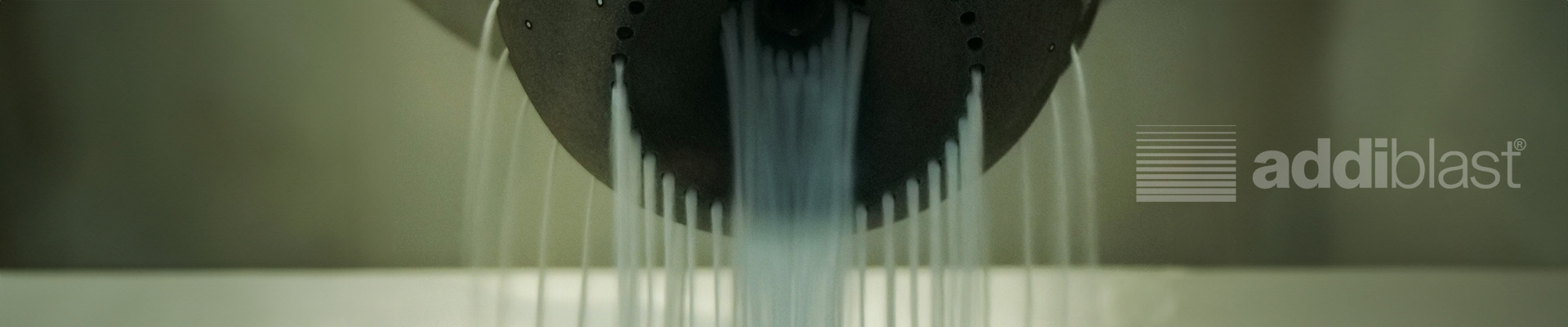
Challenges of Post-Processing in L-PBF
The primary goal of Laser Powder Bed Fusion (L-PBF) technology is to create intricate and complex 3D printed parts. Within this process, residual powder is produced. The powder must be carefully cleaned to ensure the integrity, value, and look of the final product. The presence of unremoved powder may result in internal stress areas, decreased mechanical properties, and an unfinished surface appearance. Additionally, it is crucial not to overlook the safety and environmental implications of handling and disposing of metallic powders, especially those that are highly reactive
Statistical data and industrial research demonstrate the economic ramifications of ineffective post-processing. In severe cases, trapped powder may constitute up to 20% of a parts weight. For example, if a part weighs 60 kilograms, it could contain 12 kilograms of powder trapped within internal channels. Given the high cost of metal powders used in L-PBF, inefficiency can have a significant financial impact. This is where Addiblast depowdering solutions come into play. Our machines effectively remove all trapped powder from complex channels, reducing costs, time, and the need for manual labor.
Addiblast Post-Processing Solutions

At Addiblast, we address these difficulties with an entire range of solutions designed to improve the efficiency, safety, and quality of post-processing operations. Our methods are based on innovation, automation, and customization, guaranteeing that each solution is not only successful but also meets our clients’ individual requirements. Its compatibility with all major 3D printer brands makes MARS ideal for post-processing prints under defined inert conditions at maximum safety levels.
- Customization: Providing specialized de-powdering solutions since we recognize the varying needs of different industries. With this method, we may customize our technology to meet the particular requirements and difficulties of any project, improving the post-processing workflow’s efficiency. Currently, we offer a build volume of up to 1000 x 1000 x 1000 mm (1m³), with weights reaching 1100 kg or even more if requested by clients.
- Automation: Improving precision and repeatability in our de-powdering procedures by utilizing automation. Our automated technologies are developed to reliably produce excellent results while minimizing the variability that comes with manual post-processing techniques. This not only guarantees that every component satisfies the highest requirements but also optimizes the process, saving a significant amount of money and minimizing the need for manual labor.
- Industry 4.0 Principles: Our post-processing equipment has advanced data analytics and networking capabilities that enable real-time de-powdering process monitoring and optimization. Continuous improvement and efficiency are of the highest priority in the production environment, which is made more intelligent and responsive by this integration.
The Future of Post-Processing
The world of additive manufacturing is ever-changing, with new problems and possibilities developing at a rapid rate. This is why Addiblast is the answer to the problems of the future. We are dedicated to being at the forefront of this evolution to improve our post-processing solutions. The future holds more developments in automation, machine learning, and materials science, all of which have the potential to redefine the effectiveness and efficiency of post-processing in additive manufacturing.
Post-processing is an essential phase in the additive manufacturing process that allows L-PBF technology to reach its full potential. Addiblast is committed to solving the problems of this stage with creative, tailored solutions that prioritize efficiency, quality, and safety. As we look ahead, our focus remains on improving our technologies and procedures to match the industry’s changing needs, ensuring that our clients can continue to rely on us for their post-processing requirements.