Guide to pellet additive manufacturing
What is pellet 3D printing?
Pellet additive manufacturing or pellet 3D printing, sometimes known as fused granulate fabrication (FGF), is a variant of fused deposition modeling (FDM, or FFF for fused filament fabrication) that uses pellets as feedstock instead of filament.
Although filament is suitable for most 3D printing applications, pellet 3D printing has carved out a niche in prototyping and large-format printing, where it can offer important advantages such as lower costs and faster builds.
To use pellets as feedstock, however, one needs a special type of extruder different from the kind found on an FDM printer.
How pellet additive manufacturing works
The pellet extrusion process
Pellet 3D printing borrows aspects from both FDM and plastic forming processes like injection molding. Like FDM, it builds up parts layer by layer by extruding molten material from a nozzle attached to a computer-controlled printhead.
Where it differs from FDM, and where it more closely resembles injection molding, is the way it feeds raw material to the nozzle, which it does via a screw and barrel system. In this system, pellets are gravity-fed from a hopper into a heated barrel, where they are melted down and forced towards a nozzle by a reciprocating screw (or auger).
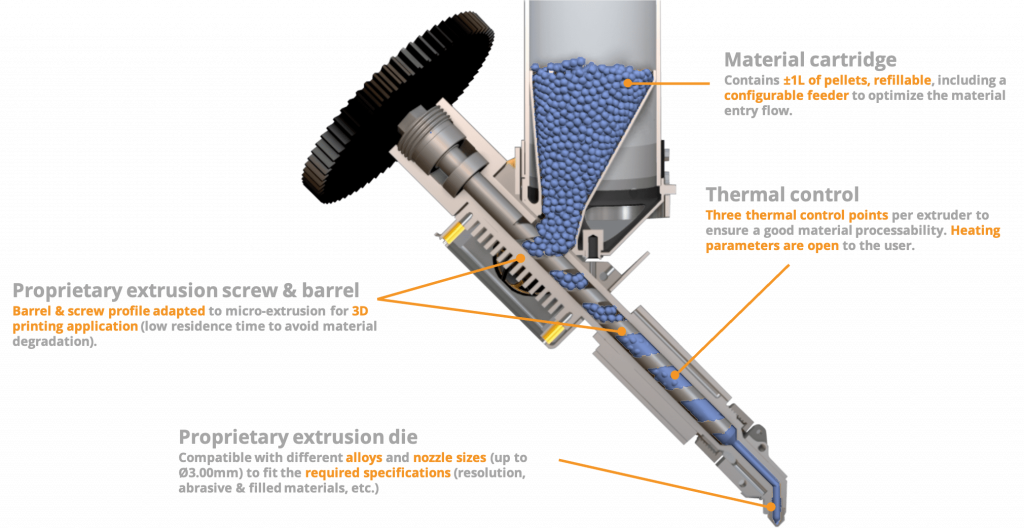
Compared to FDM, pellet additive manufacturing offers fast speeds and large nozzle diameters, but falls short in terms of accuracy and resolution.
Pellet feedstock
Mass-produced thermoplastic pellets, which may also be called nurdles or granules, typically come in a spherical or cylindrical shape and have a diameter of a few millimeters.
Many plastics (as well as metals and composites) are manufactured in pellet form, and pellets are typically 60–90 percent cheaper than an equivalent 3D printer filament. Because pellets are required for other plastic manufacturing processes like injection molding and plastic extrusion, they are both ubiquitous and affordable.
Advantages of pellet 3D printing
The benefits of pellet 3D printing include large-format 3D printing and low material costs compared to FDM.
Material cost
Pellets are easy and economical to manufacture in huge volumes and consequently have a low retail price. Filament is more expensive because it takes longer to produce (it is usually extruded from pellets) and provides a high level of convenience for FDM users.
Range of materials
A wide variety of plastics is available in pellet form, including many recycled plastics, and some materials are easier to make into pellets than filament due to their chemical composition.
Qualified materials
Pellet feedstock is widely used in conventional manufacturing processes such as plastic injection molding. Hence, manufacturers who are already using pellets– and in materials that they have qualified for their own applications– can use the exact same materials with their pellet additive manufacturing systems.
Large-format printing
Pellets can be fed into a hopper continuously without interrupting the print, which is useful for printing large objects. Conversely, if a large-format print requires more than one spool of filament, the filament must be switched mid-print, which can lead to imperfections.
Fast printing
Pellet extrusion with its barrel and screw system enables fast flow rates and deposition rates. Nozzles can also have wider diameters, which allows more material to be extruded in a shorter space of time. Pellet 3D printer manufacturer Juggerbot3D estimates that pellet extruders could have a maximum throughput up to 80 times greater than filament extruders.
Limitations of pellet 3D printing
3D printing filament is costly for a reason: it allows for a level of control and precision beyond the capabilities of pellets.
Resolution and complexity
Pellet 3D printing cannot achieve resolutions comparable to FDM. For a typical machine, the smallest layer height achievable in pellet printing is about 1 mm (1000 microns). Part complexity is limited, and overhangs are not possible.
Flow control
Melting and extruding plastic with a reciprocating screw is great for pumping out large volumes of material, but it offers a lower level of control than a stepper-motor filament extruder. For instance, it is impossible to retract the extruded material, which can lead to oozing.
Machine size
Pellet extrusion systems can be heavy and occupy a large footprint, making them less convenient than some FDM printers.
Overview of available pellet AM technologies
Pellet 3D printing requires either a dedicated pellet 3D printer or a pellet extruder that can be fitted to an existing machine.
Some pellet 3D printers offer a large build volume suitable for applications like architectural printing or furniture production, while others are comparable to standard FDM machines. Examples of pellet printers include the large-format Cincinnati Incorporated MAAM ($155,000+), the medium-format AIM3D EXAM 510, and the compact Pollen AM Pam Series P ($65,000+).
An alternative strategy is to purchase a pellet extruder that can be fitted to a standard open-source 3D printer like a RepRap. One such extruder is the Pulsar from Dyze Design ($9,000).
It is also possible to buy a standalone filament extruder that melts pellets and turns them into filament for use with an FDM printer. Brands include Filabot (high-end, $2,700+) and Filastruder (kit, $300). Extruding filament from pellets is time-consuming but allows one to take advantage of pellet prices while retaining the printing characteristics of FDM.
Who is pellet 3D printing for?
3D printer users who find themselves limited by the throughput, build envelope, or material cost of FDM may find that pellet 3D printing is a better option for them — just as long as they are willing to sacrifice resolution and part complexity.
Manufacturers that already use pellets with their other production machines can also benefit from adding a pellet 3D printer to their arsenal, as they can use the same, qualified materials across different systems.
Pellet 3D printers are available at a wide range of price points, with solutions for casual, professional, and industrial users.