The advantages of metal AM over injection molding
Metal additive manufacturing (AM): the basics
What is metal AM?
Metal additive manufacturing (AM) is a manufacturing technique for making metal parts in a layer-by-layer fashion. Different forms of AM exist to print metal materials, the most prominent of which is powder bed fusion (PBF), which includes processes like direct metal laser sintering (DMLS) and selective laser melting (SLM).
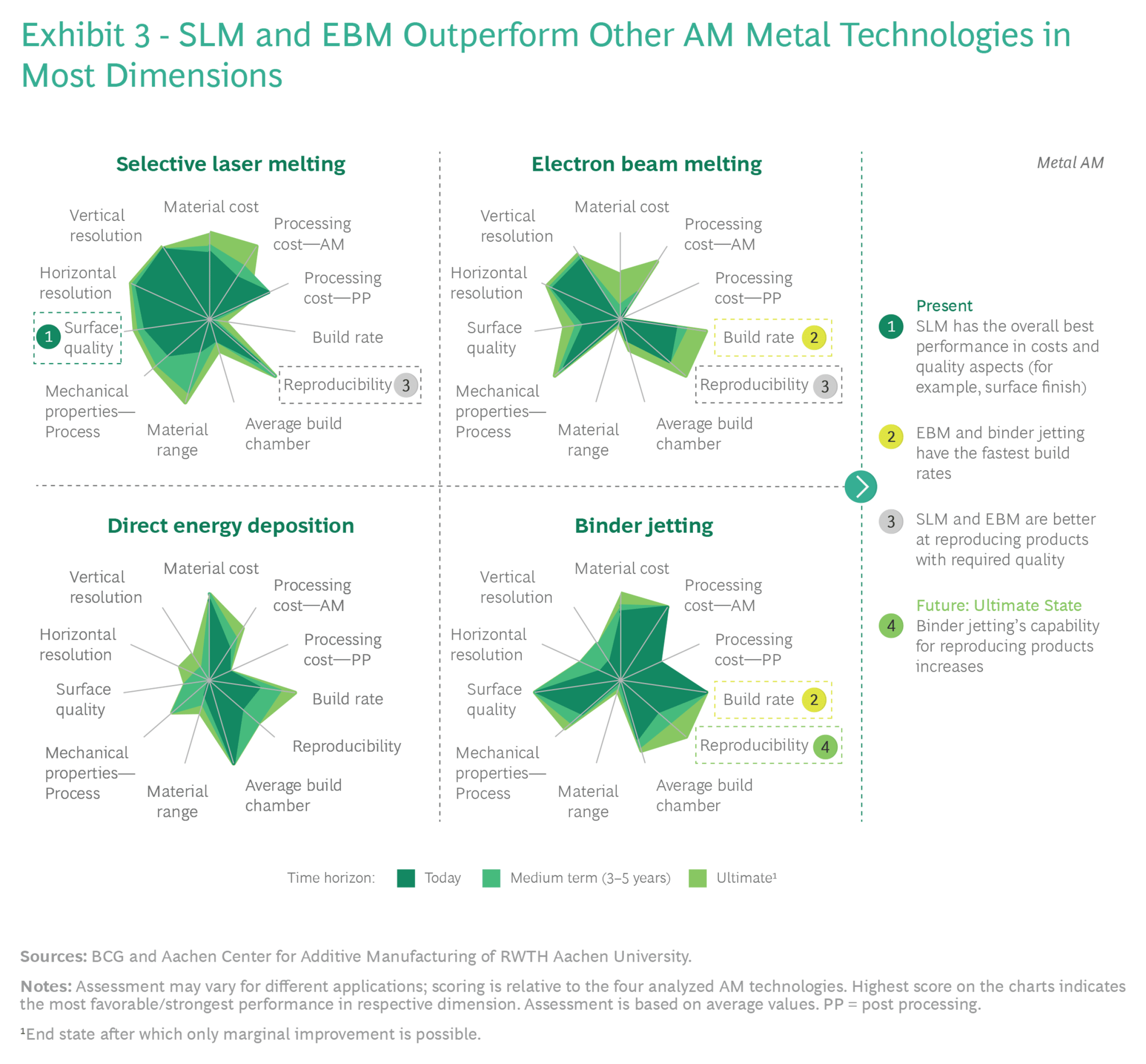
Benefits of metal AM
One of the principal advantages of metal AM is design freedom. Because parts are built up layer by layer (and not formed in a mold), they can have virtually any shape, with features like fine details, cavities, interlocking sections, and thick or thin walls.
This means that components can potentially undergo part consolidation — several connecting components are replaced by a single, functionally equivalent part — leading to part count reduction and reduced assembly time.
Another advantage is that metal AM has fewer manufacturing steps than MIM. Molding entails the making of the mold and the forming of the moldings within it. Metal AM does not require tooling (fabricating parts directly instead), making it significantly faster for one-off parts or small batches. Both processes also require post-processing steps like sintering.
The absence of tooling also makes it easy to modify the design of metal AM parts. Digital designs can be adjusted right up until the point of production, whereas tooling cannot easily be adjusted once it is made. Similarly, multiple iterations of a part can be printed at no added expense.
Metal injection molding (MIM): the basics
What is MIM?
Metal injection molding (MIM) is a form of injection molding that uses metal as a feedstock (though MIM pellets are actually a combination of metal powder and thermoplastic binder). Pellets are heated and forced into a metal mold, and the solid parts are removed once cool. They are then sintered to remove the binder and increase density.
The video below offers a comprehensive overview of how MIM works:
MIM benefits
The principal advantages of MIM are high throughput and economy of scale. Once a mold has been produced, it can be used to make thousands of duplicate parts, with the cost-per-part reducing as the quantity increases. With metal AM, there is no such economy of scale: printing thousands of identical parts is inconvenient and does not result in a lower cost-per-part.
Mass production with MIM is not just affordable; it is also fast. Although mold production and material preparation can take several weeks, each injection or “shot” takes a matter of seconds. The speed is somewhat counteracted by sintering times, but several parts can be sintered in the same furnace.
Additionally, MIM produces a slightly superior surface finish compared to AM, with less noticeable roughness. That being said, neither process can match the finish of a CNC machined part, and machining is often required as a post-processing step.
Differences between AM and MIM part design
There are certain situations where either AM or MIM could be used to make a metal part. However, each process requires its own unique design considerations; it can be difficult to turn a part designed according to the principles of DfAM (design for additive manufacturing) into a moldable part, and it can also be difficult — albeit less so — to turn a MIM design into a 3D printable part.
On the whole, metal AM has fewer design constraints than MIM, and PBF specifically has fewer constraints than many other forms of AM, since unsintered powder helps support parts during printing. Wall thicknesses should generally exceed 0.5 mm, unsupported overhangs should be more than 45° from the horizontal to prevent collapse, and, if using a PBF process, escape holes should be implemented so that unsintered powder can be removed.
Design considerations for MIM are different, because the need to eject parts from a mold limits possible shapes. Internal features and channels, for example, must be ruled out, while overhanging sections — while possible — necessitate expensive multi-component molds with sliding sections.
Other rules to follow during MIM design include maintaining even wall thickness and eliminating sharp corners with fillets and radii. (Conversely, squared-off corners may print more easily than rounded ones when using metal AM.) Engineers must also consider factors like gate placement, parting lines, and feature orientation.
When to choose AM over MIM
In many cases, the choice between AM and MIM comes down to production volumes. Put simply, AM is cost-effective — and therefore the better choice — for prototyping and low-volume production, while MIM is more cost-effective in higher volumes. Identifying the point at which MIM becomes better value is, of course, easier said than done; it’s generally comprised between 20,000 and 50,000 units.
If quantity is not a deciding factor, there are other reasons why one might choose AM over MIM.
For instance, complex designs tend to favor metal AM, since the geometries of MIM parts are restricted by part ejection. And design freedom can in turn lead to desirable material properties such as a good strength-to-weight ratio: parts can be printed with topologically optimized interiors (lattice structures, for example) that maximize strength and eliminate surplus material.
In practical terms, the ability to 3D print complex designs makes metal AM suitable for applications in medicine (e.g. patient-specific titanium implants with porous internal geometries), aerospace (strong and lightweight jet engine components, which can even be certified), and energy (turbine blades).
Metal AM also trumps MIM in terms of part refinement. Digital designs can be tinkered with, at no cost, immediately prior to printing, and multiple iterations of a part can be printed simultaneously or in sequence. This is useful for prototyping during R&D, and also acts as a financial safety net during production, since costly tooling will not need modifying or replacing.
In-house vs external AM/MIM
Besides the question of AM vs MIM, companies may wonder whether to go with in-house manufacturing (which requires upfront investment) or use an external supplier (where the cost-per-part is higher).
Metal AM and MIM systems are both expensive ($100,000+), so the decision again comes down to production volumes. The infrequent production of small batches will likely not justify investment in in-house equipment, regardless of the technology. That being said, companies can be more flexible when working with external AM part suppliers, since they rarely specify a minimum order quantity (MOQ).
Using metal AM to assist MIM
Metal AM and MIM need not be considered rival processes. In fact, metal AM can be used to complement MIM, either as a prototyping tool for parts that will ultimately be molded, or when leveraged as a mold-making technique.
Traditional molds are typically made from tool steel feedstock, which is not especially amenable to metal AM. However, titanium 3D printed molds — much cheaper than traditional molds — can also perform to a high standard.