Ultimate guide to silicone 3D printing
What is silicone and why 3D print it?
With excellent thermal stability, water resistance, and biocompatibility, silicone has long been a desirable material in additive manufacturing (AM). Coupled with the affordability and flexibility of 3D printing, silicone offers exciting possibilities in healthcare, electronics, and other fields.
Until recently, however, silicone had been almost impossible to print. Unlike extrusion-friendly thermoplastics, pure silicone cannot be melted into a liquid and then be re-solidified, which means it cannot be fed through an ordinary FFF 3D printer. The material had therefore been restricted to traditional manufacturing processes like injection molding.
All of that has changed in the last five years, during which a number of companies have developed novel systems for 3D printing silicone. Some use print head deposition, while others use vat photopolymerization, producing parts comparable to injection molded parts.
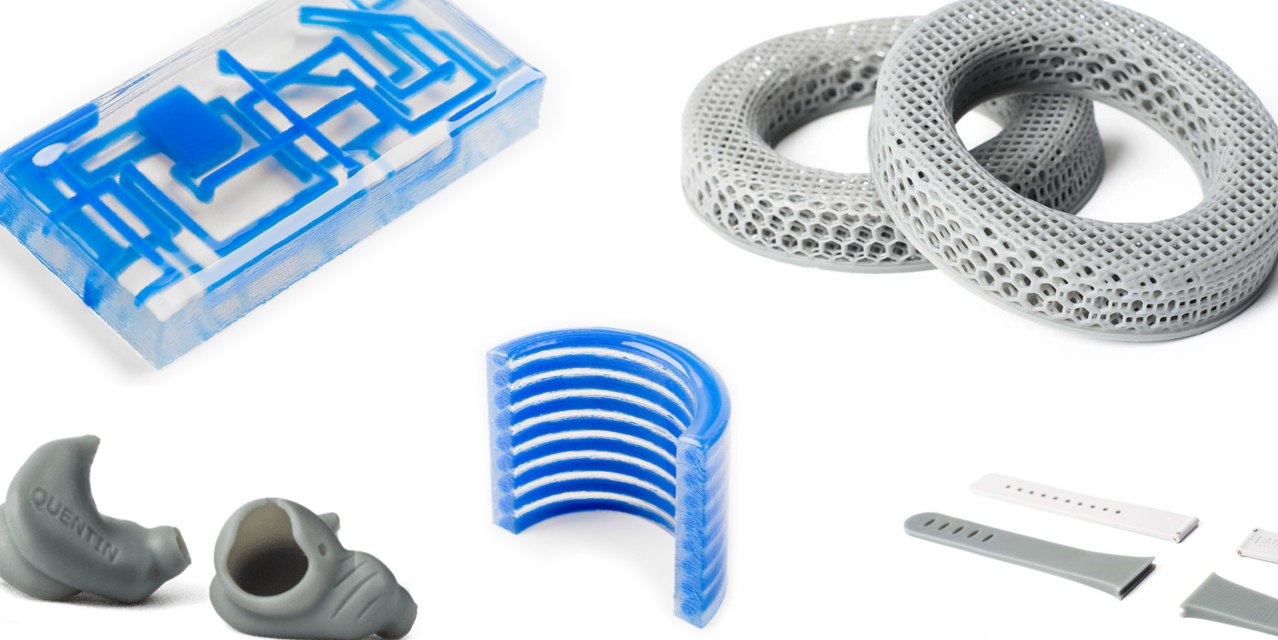
Silicone material properties
Silicones are polymers containing siloxane. They come in several forms, including oil, grease, resin, and rubber.
In 3D printing, manufacturers are mostly interested in liquid silicone rubber (LSR), a highly stable elastomer resistant to extreme temperatures and environments.
Material properties of silicone include:
- Excellent thermal stability
- Available in different hardnesses
- Water resistance and suitability as sealant
- UV resistance
- Oxidation resistance
- Compression and shear resistance
- Flame retardancy
- Electrical insulation
- Biocompatibility
- Food safe
- Can be sterilized
- Color and translucency options
It is, however, crucial to mention two important matters. First, most 3D printable LSRs (and corresponding support materials) are still in the R&D phase and aren’t commercially available yet. Second, many silicone 3D printing processes require the LSR to include UV curing agents, which weaken the silicone itself and alter its properties.
Hence, unless you are 3D printing pure silicone, you won’t be able to benefit from all of the properties listed above.
Advantages of silicone 3D printing
Many of the material properties of silicone can be considered advantages in and of themselves. However, the 3D printing of silicone also provides specific benefits.
Rapid prototyping
Making silicone parts with a 3D printer allows designers to quickly iterate silicone prototypes in an unprecedented manner. During R&D, designers can also make adjustments to their CAD design and re-print the prototype with minimal costs.
Low-volume production
3D printing enables the production of silicone parts in low volumes without high tooling costs. Since previous silicone production was often limited to injection molding, it was rarely feasible to produce in low quantities — i.e. tens or hundreds of units — because the cost of making a metal mold was too high (although that’s changing too with metal 3D printing).
New levels of customization
3D printing opens up new possibilities for customized silicone items. LSR was already widely used in the healthcare industry, but 3D printing allows for the fabrication of custom items like patient-specific implants. It also allows for the fabrication of parts like custom-fit gaskets in construction or consumer goods.
New geometrical possibilities
When designing silicone parts for injection molding, engineers must work under the constraints of parting lines, flues, clamping holes, etc. 3D printers afford greater design freedom (even when taking DfAM into account) and can create silicone parts with complex internal geometries. In microfluidics, for example, it is possible to 3D print a silicone structure containing tiny interconnected channels — a feat that would not be possible with injection molding.
Limits of 3D printed silicone
Hardware and material availability
The main limitation of 3D printed silicone is access. Only a handful of companies offer true silicone 3D printing, which means costs are high and choices of material are limited.
Need for UV curing agents
Following up on the previous point, barely any of those companies are able to 3D print pure silicone; most of them 3D print LSR with additives such as UV curing agents, which can weaken the material or reduce the quality and lifespan of the final part.
That said, these modified silicones still offer many positive properties and are suitable for a wide range of applications. Unwanted particles can also partly be removed via post-processing techniques.
Structural limitations
Leading silicone 3D printing companies have made significant advances in recent years, but the material is still by no means additive-friendly. Even the best silicone 3D printers have small build areas and aren’t necessarily able to print support structures for the silicone.
With only one print head, a silicone 3D printer will only be able to create simple, flat-sided objects with little detail or limited geometries. Stereolithography-based silicone printing technologies solve part of that problem, but the resins include UV curing agents.
Silicone 3D printing: How it works
The high viscosity and temperature resistance of silicone have made it impractical for existing additive manufacturing technologies, leading companies to develop novel solutions.
Leading providers of silicone 3D printing technology use different approaches, but most follow a two-step or three-step sequence involving deposition, curing or vulcanizing, and post-processing.
1. Deposition
Common 3D printing technologies like FFF and Material Jetting use print heads to selectively deposit material in 2D shapes, layer by layer. And although silicone cannot be melted and extruded like FFF filament, some silicone printing processes utilize deposition too.
Printers from segment leader ACEO, for example, deploy a print head that deposits individual silicone droplets which merge together into a smooth surface.
Note: Wacker’s ACEO silicone 3D printing service was shut down in late 2021.
2. Curing or vulcanizing
Uncured silicone rubber takes the form of a liquid or gel, which is easy to manipulate but not very useful for building solid 3D objects. Printed silicone rubber therefore needs to be cured, vulcanized, or catalyzed — chemical processes that form cross-links in the polymer chain — after each layer.
Some printers use UV light or heat for this stage of the process, while others use room-temperature vulcanizing (RTV) silicone, which hardens in reaction to a catalyst or another substance.
In vat photopolymerization processes like Carbon’s CLIP technology, curing effectively replaces the deposition stage, since the UV light is precisely and selectively beamed in order to create a 2D shape for each layer.
3. Post-processing
Layer-by-layer curing, vulcanizing, or catalyzing solidifies the printed silicone enough to allow the next layer to be printed, but it does fully strengthen the part.
After the silicone print has been removed from the printer, it is usually subject to a longer post-curing process, for example in an oven, which causes further chemical reactions within the silicone part and removes unwanted particles.
Parts may also need to be washed to remove support material or subjected to other post-processing techniques.
Types of silicone 3D printers
Deposition
LSR can be deposited in drops via an extruder and then cured after each deposited layer. This was the technique perfected by German company ACEO, the Wacker Chemie brand that kickstarted the current generation of silicone 3D printing technologies in 2016.
ACEO’s drop-on-demand process “deposits single silicone voxels on a building platform” which “merge smoothly into a homogeneous surface” and are platinum-cured with UV light. Support structures maintain part stability, and the finished print is washed and then post-cured with heat to “remove volatiles and achieve the final mechanical properties.”
Others use an extrusion-type print head to deposit one-component (RTV-1) or two-component (RTV-2) silicones without the need for UV curing. RTV-1 silicones require a catalyst and humidity to vulcanize, while RTV-2 silicones vulcanize when their two separate components are mixed together — achievable with dual print heads.
3D printing pure silicone is possible, though there are very few of those machines on the market.
Some low-cost silicone printers use a deposition technique that drops liquid silicone into spaces within a solid matrix, similar to 3D bioprinting technology.
Vat photopolymerization
Until recently, most developers of DLP and SLA 3D printing hardware overlooked silicone due to its challenging material properties, instead favoring silicone-like elastomeric resins with greater printability.
The CLIP process from Carbon resembles DLP 3D printing, curing parts in a vat of liquid material using UV light, but its “continuous liquid interface” creates a non-curable zone between the part and an oxygen-permeable window, ensuring that cured layers of its silicone urethane material do not stick to the window. Because layers do not need to be peeled off a build plate, CLIP can process very soft materials like silicone.
Spectroplast, a Swiss provider of silicone 3D printing services, describes its Silicone Additive Manufacturing (SAM) technology as “similar to SLA and DLP.”
Silicone parts 3D printed with vat photopolymerization are washed and post-cured to form cross-links and increase strength.
Other
French startup 3Deus Dynamics is working on a whole new type of silicone 3D printing process called Dynamic Molding Technology. Put simply, this method consists in depositing pure silicone into a static volume of powder.
The print head dives into the powder, injecting silicone — or any other material that’s compatible with injection molding techniques — as it moves around to “draw” the object’s layers. The object being printed is entirely surrounded by powder at all times, and no support structures are required (as is the case with SLS 3D printers).
Industries and applications for silicone 3D printing
Silicone 3D printing may be new, but its uses are already apparent across a number of industries, from healthcare to robotics.
Healthcare
Medical-grade silicones are a staple of the healthcare industry, being used to make items like implants, feeding tubes, catheters, respiratory masks, hearing aids, and containers. 3D printing in the medical industry provides further possibilities, particularly with regard to patient customization.
After obtaining a patient’s anatomical details, medical professionals can fabricate one-off items like silicone implants that are tailored to a patient’s body, ensuring a correct fit. One-off customization of this sort would not be feasible with injection molding due to high tooling costs.
Printed silicone is particularly useful for soft prostheses, such as ears and noses, which can be designed to fit a patient’s face.
Silicone may also be used for items like 3D printed medical tubing — for food delivery or respiratory systems, for example — with complex internal channels, or for breathable 3D printed wound dressings.
Dentistry
3D printing is widely used in the dental industry, with the most common technology being Stereolithography or DLP used with liquid resin, which offers a high printing resolution useful for items like surgical guides, casts, and even directly manufactured dental prostheses.
Silicone introduces new possibilities in dental 3D printing. Whereas most photosensitive resins produce hard parts (Formlabs offers a flexible resin but does not recommend the material for fine features), silicones can create useful soft parts like gum models, providing dental technicians with a far more realistic recreation of a patient’s mouth and allowing them to create more accurate dental devices.
Electronics
Due to its insulating properties, silicone is often used to create casings for electronic products. The material can reduce vibration in order to protect delicate components, and is preferable to cheaper plastics when the product will be subject to significant temperature variations.
3D printing opens up new design possibilities, such as the creation of overlapping channels for circuitry that could not be made with a two-part mold.
Soft robotics
The field of soft robotics focuses on the creation of robotic components that mimic living organisms, adding flexible components suitable for, e.g. medical robots or industrial grippers that will not damage the objects they grip.
Developers of soft robotics can use 3D printed silicone in a number of ways, either for on-demand prototypes or end-use parts. Silicones are good electrical insulators and have thermal stability, making them suitable for tough industrial use, while they can also be biocompatible — ideal for medical robots.
Soft robotic devices are often developed in a research setting, and 3D printers cater to the need to fabricate one-off experimental items.
Industrial
Silicone 3D printing has several applications in industry, such as the creation of seals and gaskets for preventing fluid leakage.
Although seals and gaskets are often manufactured in high volumes via injection molding, 3D printing allows manufacturers to prototype and test different iterations of these items to ensure good performance. 3D printed silicone seals and gaskets can be made quickly and cheaply, accelerating time-to-market for the manufacturer.
Silicone seals and gaskets are important for other industries too, including automotive, marine, and healthcare.
Silicone 3D printing service
Silicone 3D printing hardware costs tens of thousands of dollars or more, and is therefore limited to developers, researchers, and large companies — if available for purchase at all.
However, individuals and small businesses can upload their CAD designs and order printed silicone parts through a silicone 3D printing service.
Providers of silicone 3D printing services include:
- ACEO, based in Germany, is a Wacker Chemie brand and developer of the market-leading silicone 3D printing process. It responds to Requests for Quotation within 48 hours and will complete production within 10 days. Parts can be up to 200 cubic centimeters in size.
- Spectroplast, based in Switzerland, offers a vat photopolymerization silicone 3D printing process with a focus on biocompatible medical parts. It will complete production within seven days for the first part.
- Silinnov, based in France, offers a deposition-style silicone 3D printing service using Lynxter 3D printers. It can fabricate larger parts than comparable services — up to ⌀390 mm x 600 mm.
Indirect silicone 3D printing: Silicone molding
Before direct silicone 3D printing technology gained traction, it was still possible to fabricate high-quality silicone parts using a 3D printer: by 3D printing molds and filling or injecting them with liquid silicone.
This approach is more accessible than direct silicone 3D printing, albeit slower, since it requires several steps.
To create a 3D printed mold suitable for silicone molding, the CAD design for the part must be inverted and adjusted, forming a container into which liquid silicone can flow. A mold generally requires a parting line, injection ports, locators, and clamping holes.
A heat-resistant 3D printing material like ABS makes a good mold, since it needs to withstand the curing process at around 70°C. Once the mold is printed and ready, mold release spray is applied to the inside and liquid silicone can then be poured into the mold. Curing takes around an hour and a half.
Alternatively, silicone can be used as a material for the mold itself. By 3D printing a master of a part (from any material) and then immersing it in liquid silicone, one can make a silicone mold suitable for duplicating the printed master. The flexibility of silicone makes it easy to release solid molded parts from within the mold.
FAQ
Most dedicated silicone 3D printers cost upwards of $30,000, with some as much as $150,000. Printers developed by segment leader ACEO are not available for general purchase.
3D printing thermoplastics like TPE and TPU offer desirable properties like good impact strength, tear resistance, and shock absorption. They are suitable for many applications, but silicone has greater elastomeric properties.
Spectroplast, a 3D printed silicone service bureau, estimates that silicone 3D printing is cheaper than injection molding in quantities of up to around 6,000 units, after which injection molding becomes cheaper.